Unlocking the Potential of Drilling Float Valves
Introduction:
The drilling float valve plays a critical role in maintaining wellbore integrity and optimizing drilling operations. This article provides a professional overview of drilling float valves, covering their material, manufacturing process, international inspection standards, working principle, and maintenance methods. Additionally, essential parameters are presented in readily accessible tables for easy reference.
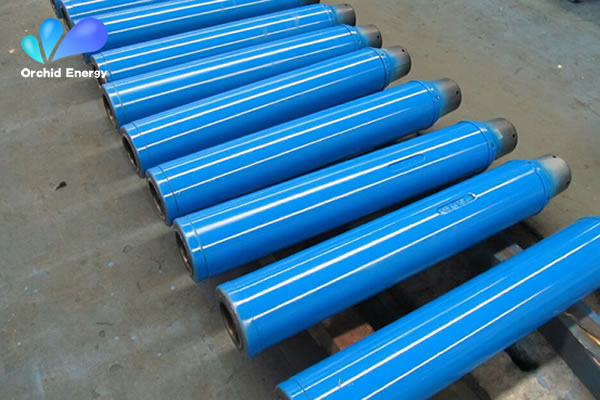
1. Material Selection:
Drilling float valves are typically manufactured using high-quality materials that offer durability, corrosion resistance, and reliable performance. Common materials used for float valve construction include:
Table 1: Material Specifications for Drilling Float Valve Components
Component | Material |
Body | Stainless Steel |
Flapper | Nitrile Rubber |
Seat Ring | Tungsten Carbide |
Springs | Stainless Steel |
2. Manufacturing Process:
The manufacturing of drilling float valves involves several steps, ensuring precise dimensions and reliable functionality. The typical manufacturing process includes:
Table 2: Steps in the Manufacturing Process of Drilling Float Valves
Step | Description |
Material | Procurement and quality check |
Machining | CNC machining of components |
Assembly | Integration of components and testing |
Coating | Corrosion-resistant coating or plating application |
Quality Check | Inspection for dimensional accuracy and functionality |
3. International Inspection Standards:
To ensure the quality and reliability of drilling float valves, various international standards are followed during manufacturing and inspection processes. Common standards include:
Table 3: International Inspection Standards for Drilling Float Valves
Standard | Description |
API 10D | Specification for Drill-through Equipment |
ISO 10427-1:2010 | Petroleum and natural gas industries - Equipment for well cementing - Part 1: Casing Float Equipment |
NACE MR0175-2003 | Petroleum, petrochemical, and natural gas industries - Material for use in H2S environments |
ASME B31.3 | Process Piping |
4. Working Principle:
The working principle of drilling float valves is based on differential pressure across the valve. When the drilling fluid pressure from the wellbore surpasses the pressure on the opposite side of the valve, the valve opens to allow fluid flow. Conversely, when the pressure differential is reversed, the valve closes to prevent backflow.
5. Maintenance Methods:
Regular maintenance and inspection of drilling float valves are essential to ensure optimum performance and longevity. Common maintenance methods include:
Table 4: Maintenance Methods for Drilling Float Valves
Maintenance Task | Description |
Cleaning | Removal of debris and mud from valve components |
Inspection | Visual inspection for wear, corrosion, or damage |
Lubrication | Applying appropriate lubricant to ensure smooth valve operation |
Pressure Testing | Verifying valve functionality under specified pressure conditions |
Replacement of Seals | Replacement of worn or damaged seals to maintain integrity |
Conclusion:
Drilling float valves are crucial components in drilling operations, ensuring the integrity of the wellbore and efficient fluid flow control. Understanding their material, manufacturing process, international inspection standards, working principle, and maintenance methods is essential for successful drilling operations. By adhering to international standards and following proper maintenance procedures, drilling float valves can provide reliable and long-lasting performance in demanding drilling environments.
Tags: Float sub & Float valve
In this article, we provide a detailed overview of drilling float valves, focusing on materials, manufacturing, and maintenance. By exploring these key aspects, readers will gain insights into optimizing drilling operations and enhancing overall performance.
2023-08-10